The End of Lean Production… and What’s Ahead
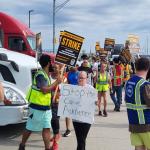
For three and a half decades, lean management drove the production and movement of goods. But now logistics and manufacturing employers are shifting to a new model. To maximize our leverage, workers should understand it.
Lean production, introduced in the 1980s from Japanese automakers, caught on in many U.S. industries. It was a whole bundle of techniques to maximize profit, including ratcheting up workloads and pace to the point of breakdown, and inviting workers to brainstorm ways to increase their own exploitation.
A central component was “just-in-time” (JIT) delivery, so companies weren’t spending to make extras or store anything until it was needed. Even within a plant, parts and supplies would arrive exactly when, where, and in the quantities they had to. Manufacturing productivity in the U.S. increased about 4 percent a year until the Great Recession of 2008-2010.
But then it collapsed, reflecting the exhaustion of lean production and its tech. The annual increase in manufacturing productivity was lagging by 2019. It rose again in 2021 as the pandemic eased, but then fell again in 2022 and 2023.
The “management-by-stress” methods weren’t working anymore. “Multifactor Productivity,” a Bureau of Labor Statistics measure of the impact of tech advances, streamlined organization, and increases in worker effort and management efficiency, dropped after 2010 to its lowest level since the crisis-ridden, pre-lean 1970s.
Technology also failed to improve worker output. A 2020 International Labour Organization study of auto plants in the U.S., Germany, and China found that the introduction of automation and robotics had “not been very successful” in restoring productivity and was often abandoned.
After a brief productivity increase in trucking and warehousing following the Great Recession, productivity in these sectors collapsed too. As of 2016, delivery times from U.S. suppliers to businesses were rising.
BUSINESS THINKS TWICE
The pandemic pushed delivery times even longer. The Covid- and climate-driven “supply chain crisis” of 2021-2022 revealed just how vulnerable to disruption JIT was and finally led businesses to reconsider some of the major aspects of lean production—above all just-in-time delivery and depending on just a single supplier.
Shippers turned to holding more inventory. The industry magazine GlobalTranz noted in its 2022 logistics report that, “given the potential for delays, lean strategies have proven too rigid.” Citi CPS reported that as of 2023, corporations were switching “from a just-in-time to a just-in-case approach.”
A 2023 Accenture survey of more than 1,200 companies revealed that 42 percent had already moved from JIT to multiple sourcing, and 72 percent planned to do so within three years.
The importance of JIT had been that it reduced costly inventory, whether of parts or of finished products. Now, as productivity fell and delivery times rose, inventories grew by an average 4.3 percent annually from 2010 to 2019, and then faster, 7.1 percent annually from 2019 to 2022 as companies began to switch to just-in-case. This hurt profit rates and company competitiveness, domestically and internationally.
AMAZONIFICATION
How could companies get the advantages of just-in-case without the high inventory costs? The answer was found in the means that propelled Amazon’s rapid growth: keeping inventory relatively low by rapidly moving millions of products to thousands of locations. As its sales increased fivefold, from 2015 to 2022, Amazon’s inventory-to-sales ratio fell from 9.3 percent to 6.7 percent.
The twin secrets to its success were a brutal labor process, in which tasks and pace are directed by algorithms, and an increasingly dense logistics system. By 2023 the journal Transport Topics ranked Amazon as the number one global freight carrier.
Amazon’s trick is to get payment from customers, mostly by credit card, before it pays the vendors whose products it sells. The revenue it earns in this time gap it calls its “free cash flow,” a disguised form of otherwise taxable profits, because while Amazon is holding this money it can use it to buy more goods and expand facilities in order to make even more money. In 2022, Amazon made $12 billion in “operating income” (declared profits), but also drew in $11.6 billion in “free cash flow.”
But to make this work it must move things rapidly and continuously. This is neither just-in-time nor just-in-case.
Amazon has developed a dense logistics system that maximizes the velocity at which all products move constantly within and between locations. Besides fulfillment centers, in 2014 it added Prime Hubs and sortation centers, and in 2016 delivery stations.
The number of fulfillment centers more than doubled, from 139 in 2018 to 349 in 2022. Sortation centers tripled from 47 to 140 over the same period. Delivery stations, the last stop before the customer, grew sevenfold, from 87 to 656. Next Amazon is planning to build 150 “ultrafast delivery hubs.”
These facilities are concentrated in major metropolitan areas, close to large labor markets and lucrative consumer markets. As Amazon VP Udit Madan told the Wall Street Journal, “The doubling of footprint really allowed us to have a lot more facilities that were closer placed to customers.”
By 2022 Amazon had a fleet of 70,000 vehicles, and it is planning to purchase 100,000 electric vans. Most of these are driven by contingent drivers under its Flex program or those working for contractors called Delivery Service Providers. By 2021 it incorporated 42 regional airports for longer-distance rapid delivery.
DENSE, FAST, VULNERABLE
This highly orchestrated and optimized model is now shaping logistics for the U.S. economy as a whole.
Companies like Target are following Amazon’s lead, seeking to control inventory levels and outpace their rivals by creating dense networks of facilities and adding vehicles. Across the U.S., the number of trucks, warehousing and trucking facilities, and workers in these jobs are all growing at accelerating rates.
Facilities are clustered around big cities. A 2021 survey by McKinsey of “global supply-chain leaders” found that almost 90 percent “expect to pursue some degree of regionalization in the next three years”—meaning more products will be produced closer to the customer. A 2023 poll by Accenture indicated that 38 percent of executive respondents were already mostly sourcing regionally, and 65 percent planned to do so in the next three years.
These regional systems are connected by railroads and interstate highways. To better coordinate them, CITI GPS reported in 2023, companies are seeking “control tower” visibility over their supply chains—intensifying the digital surveillance, routing, and tracking of goods and labor.
These changes all put more pressure on the workers. But what is also taking shape, as companies abandon lean methods in favor of digital technology, is a system with more “nodes” and “links”—points of connection, transfer, or exchange that are activated by human labor both within and between plants, warehouses, and other facilities.
As John Womack put it in his recent book Labor Power and Strategy, “any product that moves now, anybody who moves, goes through more connections in chains and networks than a generation ago.” Each of these points is vulnerable to worker action—disruption there will cost revenue and create costly pile-ups of inventory. Workers stationed at such points have what Womack calls “positional power.”
This is true of the Amazon fulfillment center “picker” who feeds automated conveyors; the team that loads a truck; the driver of a truck or train; the assembly-line workers whose speed determines the speed of those behind them; the maintenance workers who keep mechanical or digital devices working; and so on through the workforce.
The exercise of positional power can put the brakes on the velocity of inventory, goods, and revenue to make strikes and work-to-rule actions more effective. The trick is to find the points of vulnerability, a task that calls for collective decision-making and coordination between workers.
This isn’t really a new idea. The Flint sit-down strike that brought General Motors to its knees in 1937 won recognition for the United Auto Workers because the workers seized the key Chevy 4 engine plant that supplied the other plants in Flint and beyond. With today’s tightening of supply chains and the proliferation of vulnerable points in both production and transportation, this type of strategic thinking and acting can aid not only in winning gains for union workers but also in organizing the unorganized.
That’s important, because the reconfigured production and logistics workforce is mostly non-union, often contingent or part-time. Last year the number of private sector union members grew by 191,000, and 70 percent of these worked in manufacturing or transportation and warehousing.
Many workers in these sectors are people of color, and the vast majority of those who unionized were Black or Latino and young workers, who tend to be more pro-union.
The number of workers forming unions by National Labor Relations Board-supervised elections is growing, but it’s still far too slow to change the balance of power at the heart of the economy. The collective awareness and coordinated use of positional power offers a powerful alternative route—and an additional organizing tool.
Kim Moody is a founder of Labor Notes and author of many books. He lives in London and is a member of the National Union of Journalists.